Selecting the Right Defoamer for Your Details Application Demands
Selecting the ideal defoamer for details application requirements is a nuanced process that demands careful consideration of numerous variables, such as the foam type, operating, and tool conditions. Comprehending the subtleties of defoamer performance-- consisting of rate and determination-- while also making up governing and environmental variables is crucial. Additionally, participating in tests and seeking advice from with suppliers can supply useful understandings. Nevertheless, browsing these complexities can be difficult, and the repercussions of a bad choice might be substantial. What methods can be used to ensure an ideal option?
Comprehending Foam Development
Foam formation takes place when gas is trapped within a fluid, developing a steady framework of bubbles. This sensation can considerably impact different commercial procedures, particularly in fields such as food production, pharmaceuticals, and wastewater treatment. The visibility of foam can hinder blending, reduce item quality, and also lead to functional inadequacies.
Foam commonly creates because of a combination of aspects, consisting of surface-active representatives, agitation, and the features of the liquid phase. Surfactants reduced the surface area stress of the liquid, helping with the formation of bubbles that can integrate and maintain. Agitation, whether from mechanical mixing or gas introduction, improves bubble development, bring about increased foam volume.
Recognizing the auto mechanics of foam formation is important for sectors aiming to maximize their procedures. By recognizing the specific conditions that advertise foam generation, companies can execute strategies to reduce its effects. This knowledge prepares for selecting appropriate defoaming agents that effectively target the distinct difficulties positioned by foam in various applications. As a result, an extensive understanding of foam formation is necessary for enhancing performance and preserving product integrity throughout different industries.
Sorts Of Defoamers Available
Numerous kinds of defoamers are readily available to attend to the challenges postured by foam in industrial applications. defoamers. Broadly identified, defoamers come under 3 classifications: silicone-based, non-silicone-based, and natural defoamers
Silicone-based defoamers are renowned for their effectiveness and stability throughout a variety of temperatures and pH levels. They are generally made use of in applications where solid foam suppression is needed, such as in finishings, adhesives, and paints. Their low surface area tension permits rapid foam collapse.
Non-silicone-based defoamers, typically made from organic compounds, provide a choice for applications conscious silicone deposits. These defoamers can be additional split right into polyether and ester kinds, each tailored to satisfy details formula needs. Non-silicone defoamers are frequently utilized in food handling and individual care products due to their compatibility with various formulations.
Natural defoamers, stemmed from plant or animal sources, are obtaining grip as a result of their environment-friendly profile. These items are specifically appealing in applications where regulative conformity and sustainability are paramount, such as in agrochemicals and biotechnology.
Selecting the ideal kind of defoamer is important for maximizing efficiency and making certain compatibility with specific applications.
Trick Application Factors To Consider
When picking a defoamer, it is vital to take into consideration the specific application requirements to make certain optimum performance. defoamers. Different sectors have distinct needs, such as food handling, pharmaceuticals, or wastewater treatment, and each application may call for unique defoaming buildings
Trick aspects to evaluate consist of the tool in which the defoamer will certainly be made use of, whether it is water-based, oil-based, or a combination thereof. The temperature level and pH levels of the application can additionally considerably influence the performance of a defoamer. Furthermore, compatibility with various other chemicals present in the system is crucial to avoid damaging responses that might compromise efficiency.
Another essential consideration is the lathering habits of the specific system. Understanding whether the foam creates rapidly or gradually can assist the choice of a defoamer that targets the source successfully. The wanted speed of defoaming can affect the option, as some applications call for rapid activity while others may tolerate slower defoaming processes.
Last but not least, environmental and regulative factors to consider must not be neglected, particularly in industries with rigorous compliance demands. Selecting a defoamer that lines up with these factors makes certain both efficiency and safety in the application.
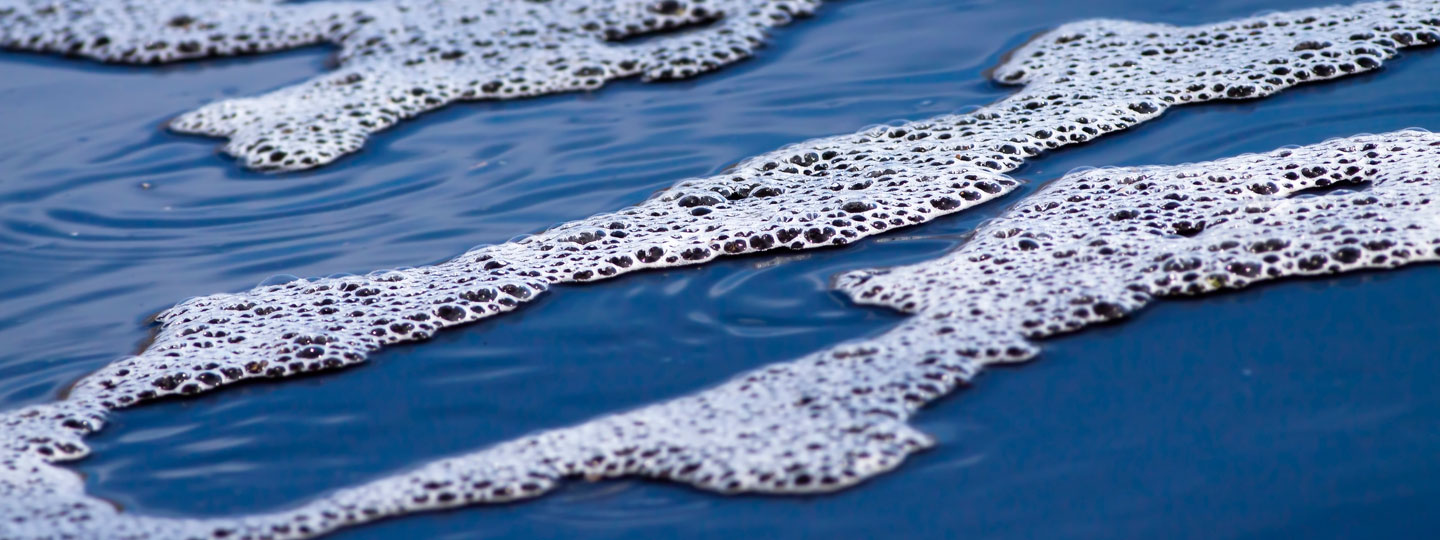
Performance Screening Techniques
Evaluating the performance of a defoamer requires an organized strategy to testing that precisely measures its performance in details applications. Various efficiency testing techniques can be utilized to ascertain the optimal defoamer for a given solution.
One usual method is the bubble examination, which evaluates the defoamer's capability to reduce foam quantity over time. This examination involves producing a steady foam and then including the defoamer to observe the rate of foam collapse.
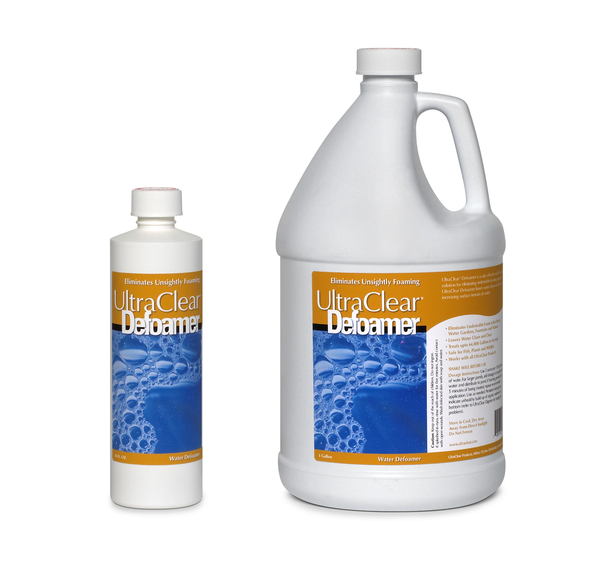
Eventually, picking the appropriate performance testing technique depends upon the certain application and the type of foam being dealt with. Each technique provides useful data that can assist solution modifications and improve the effectiveness of the defoamer in practical applications.
Finest Practices for Option

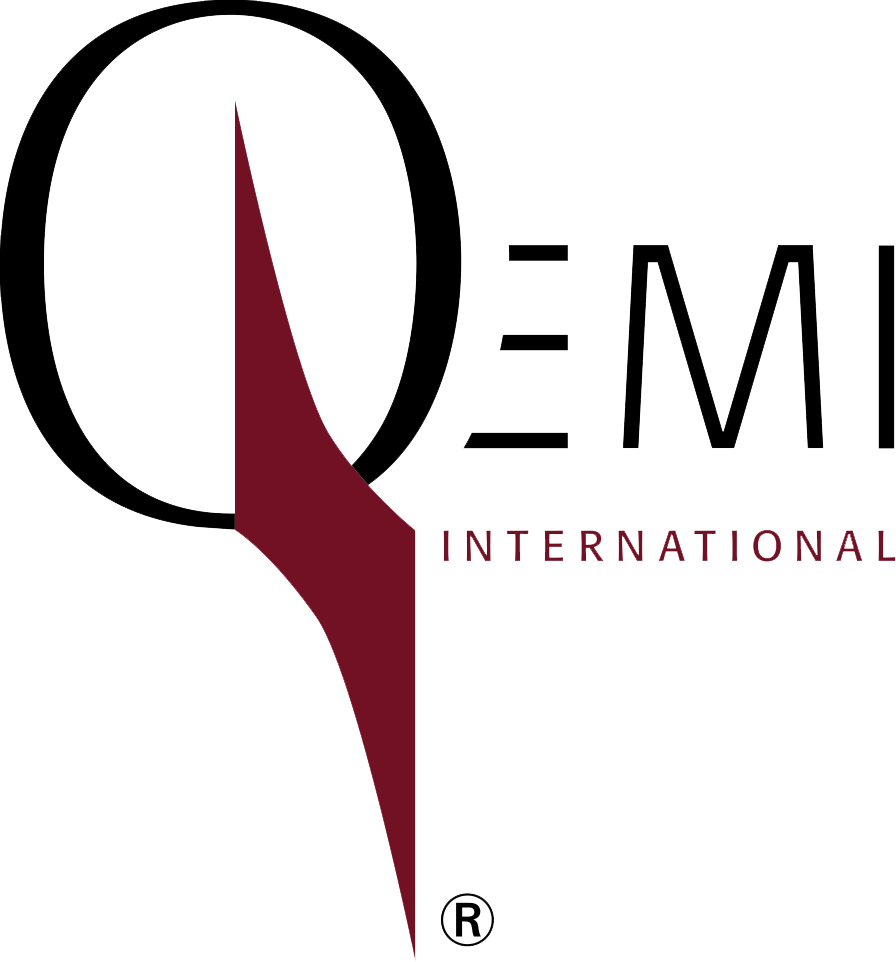
Next, consider the defoamer's performance in terms of rate of action and determination. A quick-acting defoamer may be essential for procedures where fast foam reductions is vital, while a much more relentless solution may be required for prolonged foam control. Furthermore, examine the ecological impact of the defoamer, including its biodegradability and any type of regulative compliance demands.
Conduct trials with chosen defoamers to identify their performance in real-world conditions. This action is vital to validate that the chosen product satisfies performance assumptions. Consult with manufacturers or suppliers for technological assistance and support, as they can supply important insights into item formulas and application techniques. By sticking to these ideal practices, you can enhance foam control performance and make certain the long life of your processes.
Verdict
In recap, picking the suitable defoamer necessitates a detailed analysis of various aspects, including foam kind, tool, operating conditions, and environmental considerations. Recognizing the distinct attributes of foam development and the readily available defoamer options is essential.
Choosing the suitable defoamer for details application needs is a nuanced procedure that demands cautious consideration of numerous elements, such as the foam tool, Discover More type, and operating problems.Selecting the right defoamer is important for accomplishing optimal performance in foam control applications. A quick-acting defoamer may be necessary for procedures where fast foam reductions is crucial, while a much more consistent formula may be needed for prolonged foam control.In summary, picking the suitable defoamer necessitates an extensive examination of different factors, including foam kind, tool, operating conditions, and environmental factors to consider. Recognizing the one-of-a-kind features of foam formation and the available defoamer alternatives is crucial.